
Welcome to visit: Beijing Trinova Auto Tech Co.,Ltd
Intelligent line control dynamic system solutions for advanced driving assistance!
- Categories:News center
- Author:
- Origin:
- Time of issue:2023-08-31 14:23
- Views:
(Summary description)
Intelligent line control dynamic system solutions for advanced driving assistance!
(Summary description)
- Categories:News center
- Author:
- Origin:
- Time of issue:2023-08-31 14:23
- Views:
Introduction
In the era of major changes in the automotive industry, electrification, networking and intelligence have become important areas of research and development, and highly intelligent new vehicles need to have smarter, safer and more reliable chassis actuators. The wire control dynamic technology is one of the core technologies of intelligent chassis. In order to adapt to the multi-scenario application of intelligent vehicle, the wire control dynamic system not only needs to realize the conventional braking assist function to meet the artificial braking, but also needs to have the intelligent technology such as active braking and dynamic state information prediction. After years of technology grinding and accumulation, Trinova has continuously innovated and integrated in the line control motion product series, and developed the intelligent line control motion system solution (T-IBWS) that ADAPTS to the future smart car. At present, the solution has been perfectly matched with ESC-Pro products. Based on the original dynamic control functions of ESC (ABS, TCS, AYC, etc.), it integrates ADAS support functions to provide a safe and comfortable control and execution interface for AEB, ACC, APA and other functions, and supports real-time tire pressure monitoring and vision-based pavement adhesion coefficient prediction to ensure the safety of intelligent vehicles in all aspects.
First, the rapid development of electric intelligent vehicles
As an important carrier of intelligent connected vehicles, new energy vehicles have developed rapidly in recent years with the support of government subsidy policies in China. At the same time, in order to achieve the transformation of energy consumption structure, vigorously develop new energy vehicles is also the only way. In recent years, the sales and penetration rate of new energy vehicles at home and abroad have increased year by year.
At the same time, the rapid development of artificial intelligence and the increasing popularity of vehicle electrification have prompted R&D personnel to continue to explore automotive intelligence. According to the automatic driving grade classification standard issued by the International Association of Automotive Engineers, autonomous vehicles can be divided into five levels according to the degree of intelligence. The higher the automatic driving level, the higher the control accuracy and reliability requirements for vehicles. The braking system is the core component of vehicle control, in order to meet the needs of high-level automatic driving, the line control system must have higher control accuracy, faster response speed and more comfortable subjective experience. At present, L2 advanced driving assistance system has gradually become the standard of vehicles, AEB, ACC, APA and other functions require the active braking control of the chassis braking system, that is, the vehicle can automatically slow down when there is no driver intervention. In addition, with the improvement of the level of autonomous driving, the vehicle's ability to monitor its own operating state also needs to be improved, and the vehicle needs to replace the driver for real-time observation and even prediction of the vehicle's own state information, in order to avoid risky conditions in advance, and ensure that the upper planning and bottom control can keep the vehicle in the dynamic stability range.
Second, intelligent line control dynamic system solutions
After continuous technological iterations, T-IBWS has now launched three generations of products.
T-IBWS 1.0 is the first generation intelligent wire control system solution developed to support ADAS functions. The solution currently uses ESC-Pro as the wire control actuator while retaining the basic vehicle dynamics control function, which is a low-cost, rapid production solution.
T-IBWS 2.0 adds the intelligent tire pressure monitoring system (Tri-TPMS) on the basis of 1.0, and the vehicle can actively adjust the four-wheel braking force according to the tire pressure information during high-speed emergency braking, so as to avoid serious braking deviation caused by inconsistent tire pressure on both sides of the vehicle.
T-IBWS 3.0 adds the road adhesion coefficient prediction (V-RAC) based on visual information on the basis of 2.0, which is mainly integrated in the chassis domain controller. The electronic and electrical architecture of intelligent vehicles in the future will be divided into different control domains, and the information interaction between different control areas will be stronger, and the sensor information dimension will be wider. The chassis domain will use the information of the intelligent driving domain to conduct multidimensional dynamic information observation and more accurately control the vehicle state, while the intelligent driving domain will also use the vehicle dynamics information of the chassis domain to make planning decisions and predict the dangerous state of the vehicle in advance.
T-IBWS
Based on the T-IBWS 3.0 solution, each module is introduced separately.
3. Trinova ESC-Pro system
ESC-Pro is an upgrade series of ESC-Base, which is specially developed for the underlying control of ADAS. It can meet the acceleration, speed and distance control requirements of ACC, AEB and APA. Compared with ESC-Base products, its main features are as follows:
1. Support ACC, AEB, APA and other upper ADAS functions of brake control, torque control and reasonable torque brake switching.
2. Higher deceleration control accuracy, deceleration steady state control accuracy is less than 0.2m/s2
3. Faster pressure response time, the sum of TT+TTL in AEB is less than 600ms.
4. Smaller active pressurization noise, effectively improve driving comfort.
5. With all the vehicle dynamics control functions of ESC-Base.
ESC-Pro outline diagram
ESC-P List of ro functions
Hardware scheme: hydraulic principle and design
Platform design: same hydraulic principle as Base version, shared core components, same external boundary
Series design: Provide 3ml\5ml\7ml accumulator design to meet the needs of models under 6 tons; EPBi configuration is provided
Faster active build speed: 550ms for B+class vehicle
More accurate pressure control accuracy: minimum 0.2MPa pressure control accuracy
Optimized NVH performance: Improved by more than 4db compared with the Base version
Higher life level: meet the endurance of 310,000 times limit working conditions
Software solution: ADAS supports functional adaptation
According to the requirements of the upper ADAS functions (AEB, ACC, APA, etc.), ESC can provide the support function of the executive layer, according to the upper control instructions and the actual state of the vehicle, ESC coordinates the engine torque and the pressure of the hydraulic control unit, ensuring the accuracy, stability and safety of the pressure and torque control of the executive layer.
Key technologies of ESC-Pro
Take APA as an example. After finding the target parking space according to the fusion information of the sensing system, the upper-layer APA function calculates a reasonable vehicle driving path through the path planning module, and sets the control objectives of horizontal and longitudinal motion according to the current vehicle position and target path. The steering system is responsible for horizontal control, and the braking system is responsible for longitudinal control. To support APA's longitudinal vehicle control, ESC-Pro integrates TCH, VLC_AP, CDD_AP, and PSC functions.
Since the upper APA directly sends the target distance to the line control dynamic system, TCH needs to plan the speed and acceleration within the range of the maximum limited speed, so that the planning curve can not only meet the accurate control of the target distance, but also reasonably limit the acceleration range, and effectively improve the comfort during parking. In this paper, the quintic polynomial path planning strategy is used to solve the quintic polynomial according to the position, velocity and acceleration information of the starting point and the target point, so as to obtain the target velocity and acceleration curves.
VLC is called Vehicle Longitudinal Control, and VLC_AP is a longitudinal control strategy aimed at low-speed parking conditions based on VLC. VLC_AP determines the type of actuator used according to the acceleration and deceleration requests provided by TCH and the current state of the vehicle. Maintain speed and distance by actively controlling engine torque or requesting braking from the CDD to adjust the required acceleration and deceleration.
VLC state machine
CDD stands for Controlled Deceleration for Driver Assistant System. Similar to VLC_AP, CDD_AP is also a braking control strategy adapted to parking conditions. In normal deceleration control mode, CDD calculates the target braking pressure of ESC hydraulic system according to the braking request of VLC, considering the deviation between target deceleration and actual deceleration. In addition, in the stop-stop-start stage of the vehicle, CDD can help the vehicle to stop comfortably, prevent the panic caused by the rapid movement, maintain the pressure of the vehicle in the static stage, real-time monitoring of the static state of the vehicle, once the vehicle occurs the phenomenon of slipping, timely active pressurization to ensure parking safety. According to the real-time torque of wheel end, the brake pressure is slowly released to improve the comfort during the starting process.
CDD state machine
PSC is a hydraulic system control module. After CDD_AP sends the target pressure to PSC, PSC realizes the wheel cylinder pressure to reach the target value by controlling the motor valve and motor. As ESC-Pro adopts the new design of solenoid valve and plunger pump, the hydraulic unit parameters inside PSC need to be re-calibrated, and each unit inside the hydraulic system needs to be accurately modeled. Real-time monitoring of the flow and pressure of ESC internal pipelines. At the same time, a reasonable pressure control strategy is set based on the target brake pressure and estimated pressure, and the duty cycle of the solenoid valve and the motor is controlled, so as to achieve accurate pressure control.
Piston pump load characteristics
Flow characteristics of booster valve
Pressure limiting valve flow characteristics
At present, the APA vehicle performance parameters based on the ESC-Pro line control dynamic system can meet the following requirements:
(1) Ensure that ESP control distance accuracy (absolute value) ≤20cm when APA distance request is 0; The minimum starting distance of vehicles is 15cm;
(2) The speed overshoot is 50% of the limit speed or the minimum of both in 1km/h; APA function supports maximum slope ≤5.5° (10%);
(3) Meet the vehicle acceleration value ≤ 1.5m /s²; Vehicle acceleration rate < 15 m/s^3;
(4) The ESP acceleration value during emergency braking is > -5m/s²; ESP acceleration value during comfort braking > -1.5 m/s²; Vehicle deceleration rate < 15 m/s3; ESP braking response time ≤500 ms during emergency braking.
Four, intelligent tire pressure monitoring system
Trinova Tri-TPMS is a new generation indirect tire pressure monitoring system (iTPMS) developed by Inventron based on its own technology. Compared with the built-in tire pressure sensor scheme, the indirect tire pressure monitoring scheme has low cost, fast calculation and easy maintenance. It only relies on wheel speed signal to realize the full function of tire pressure monitoring, but it has high algorithm requirements and large amount of calculation. Trinova adheres to the core technology of self-developed indirect tire pressure, which has overcome the above problems and has significant advantages in product performance.
Tri-TPMS Core Benefits:
1. Shorter alarm time: for 1-3 rounds of underpressure conditions can be realized in various sections of the alarm.
2. Wider speed range: The company's products can meet 1-3 rounds of undervoltage alarm function within 35-240km /h, and the speed range of four-wheel alarm can be expanded according to customer needs.
3. Faster alarm speed: For the requirements of European standards, the company's products 1-3 rounds of undervoltage alarm time is generally within 8 minutes (European standards require less than 10 minutes), 4 rounds of undervoltage alarm time within 15 minutes (European standards require less than 60 minutes).
In terms of algorithm strategy, the current mainstream indirect tire pressure monitoring algorithms include radius method and frequency method.
Radius method
Radius method features:
1, the radius of the underpressure tire is reduced, and the speed is significantly different from other tires
2, four rounds at the same time under pressure can not be monitored
3. The accuracy of working condition elimination is highly dependent
Tianjin YingChuanghui Intelligent Automobile Technology Co., LTD
Frequency method
Frequency method features:
1. The natural frequency of the circumferential rotation signal is reduced when the wheel is under pressure
2, can accurately identify the undervoltage state
3. High algorithm complexity
Tri-TPMS algorithm architecture
Trinova uses radius method and frequency method fusion algorithm and elastic computing architecture design, which perfectly avoids the inherent shortcomings of indirect tire pressure algorithm. Using radius method to identify relative tire pressure, using frequency method to identify absolute tire pressure, comprehensive consideration of the two results, quickly judge the four tire pressure state.
Condition screening strategy
Host computer calibration system
5. Prediction of road adhesion coefficient based on camera
Traditional road adhesion coefficient estimation strategies mainly use vehicle dynamics information for observation, but only when the vehicle is in contact with the road surface and the vehicle dynamics appear can the real road adhesion information be obtained, and there is inevitable lag. With the rapid development of automobile intelligence, more and more vehicles are equipped with advanced sensors such as cameras and radars. The road adhesion coefficient prediction method based on visual information uses deep learning technology to identify the road adhesion coefficient in front of the vehicle with the help of picture information provided by the front camera of the vehicle, and provides predictive information for the subsequent control strategy of ADAS. Make the control instruction in advance to avoid the mismatch between the upper target instruction and the actual execution ability caused by the lack of pavement adhesion.
With the rapid development of deep learning and the support of intelligent sensors, the pavement adhesion coefficient estimation problem is not limited to the traditional dynamic model strategy, but can be further classified as an image classification problem. Based on the high computing power platform of chassis domain controller, the convolution neural network is used to classify pavement images into different adhesion coefficient levels. It mainly includes four types of road conditions: high attachment, medium and high attachment, medium and low attachment (among which, the road adhesion coefficient 0.7-1 is high attachment, 0.5-0.7 is medium and high attachment, 0.3-0.5 is medium and low attachment, and 0-0.3 is low attachment), predicting the road condition in front of the vehicle in advance and making control intervention in advance to ensure the dynamic stability of the vehicle.
Convolutional neural network structure
peroration
At present, the autonomous driving industry is booming, the intelligent car "brain" (intelligent driving layer) is developing rapidly, the vehicle intelligence level is significantly improved, and the intelligent car "cerebellum" (chassis execution layer) can cooperate with the "brain" for accurate and safe vehicle control, which is also the core component of intelligent cars. The "cerebellum" of intelligent cars based on complete autonomy and control is a "stuck neck" problem in the domestic automotive industry. Trinova adheres to independent research and development, and has been deeply engaged in the field of on-line chassis control for many years. Represented by T-IBWS, Trinova has independently developed a number of on-line chassis series products. With line control actuators as the core, T-IBWS can fully support the underlying control requirements of ADAS functions, and has multidimensional vehicle dynamics information observation strategies to provide drivers with a safe and comfortable ride experience.
At present, T-IBWS products have been calibrated and matched in Chery, BAIC, Geely and other models, and some models have been completed in mass production, and the product has completed detailed testing and verification in durability, consistency, safety and other aspects. In addition to ESC-Pro products, the full range of Trinova line controls (T-Booster 2.0, T-IBC, etc.) can support T-IBWS.
In the future, based on Trinova's self-developed chassis domain controller, the braking, steering, suspension, drive and other chassis actuators will be coordinated control, and further introduce a more integrated and safer intelligent drive-by-wire chassis integration solution.
Trinova adheres to independent innovation and open communication, and is determined to contribute to the national automobile industry by providing first-class products and technologies to serve the autonomous and controllable strategic goals of China's automobile industry.
Recommended news
Online Message
Product Center
About Us
Beijing Office Address: Building 3, Yard 11, Rongxing North 1st Street, Beijing Economic and Technological Development Zone
Tianjin company address: Building 8, Robot Industry Accelerator, Automobile Industrial Park, Wuqing District, Tianjin
Service Hotline:022-59667907-8668
Company website:www.trinova-tech.com
E-mail: pr@trinova-tech.com
Follow Us
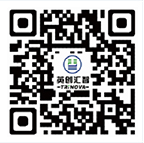
關注我們
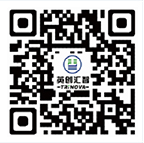
Copyright◎Beijing Trinova Auto Tech Co.,Ltd 京ICP證000000号